I’ve just launched Sequence8, a PICO-8 music sequencer toy.
Here’s a video:
You can play with it in the browser at https://billiam.itch.io/sequence8, or download prebuilt binaries.
The copy button will save your song to your clipboard so that you can keep and share them.
To import a song, just paste it in.
Shorter songs fit in a tweet, so if you make something you like, please share it with me!
I picked up PICO-8 in the enormous Itch.io bundle recently, and have been having a lot of fun with it. Sequence8 is my first PICO-8 game.
The platform’s built-in limitations help ensure that games stay small and (roughly) within scope. They can’t be too large in code length, or lexical tokens, nor in sprites, sound, or music. Audio is limited to four channels, the screen is 128px square, there are 16 colors.
Sequence8 is based on another project I never finished, built with Ruby and Gosu.
There, I was able to use several full sized audio samples of real instruments, and dynamically pitch them up. Visual effects could be handled with transparencies and complex masks. I used C libraries for fast quadtree performance for mouse events. Can’t really do any of that in PICO-8 (at least, I can’t).
Here’s some of the build process
Getting started
This is the first prototype. It can play sounds. The current beat scrolls by.
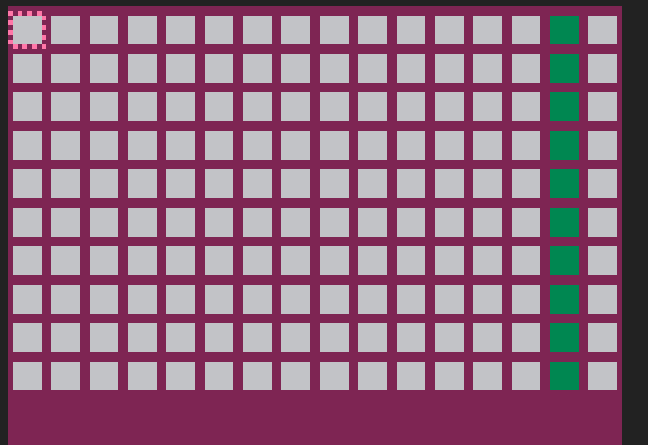
Here I’ve started adding the sprites for the background, scrub bar, and selected notes, and one of the only sprite animations.
I found this post invaluable when trying to work with PICO-8’s color palette.
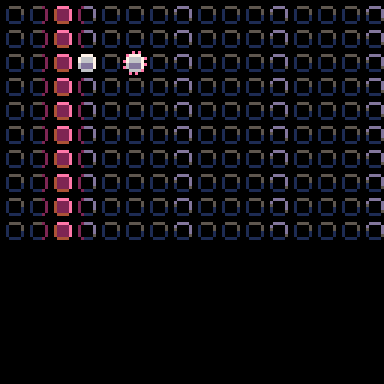
UI
Without the ability to bind a bunch of arbitrary keyboard shortcuts, I actually had to build out the UI for this as well, which took the vast majority of the project’s development time.
Challenges here were:
- Adding mouse support and mapping screen pixels to UI elements,
- having logical controller navigation for an irregular grid,
- switching between mouse and controller input without breaking something
- having a different number of notes for some instruments,
- adding and removing bars of music (which also adds and removes UI elements)
I probably rebuilt the whole UI system 3 or 4 times, and I’m still not happy with it.
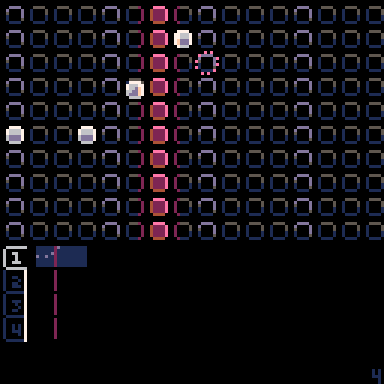
I think this didn’t work well because the tab as a UI concept implies nesting content underneath the tab, but I wanted to have more information about the other instrument tracks visible at once.
Here’s the mouse support. It’s mostly built on top of the controller support, so while the mouse has a pixel position, it also maintains a position within the UI grid, identical to controller handling.
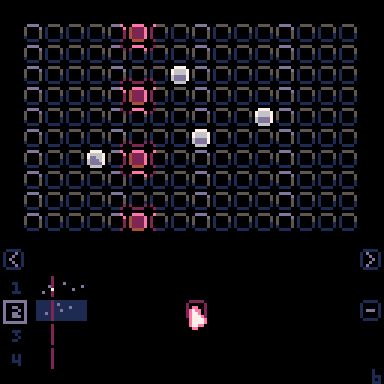
Lighting
I went through a few iterations for lighting effects. Originally, the song progress bar was represented by a full column of sprites, as well as some smaller sprites to both sides that would overlay the background to fake a glowing effect.
In this version, the notes light up for a moment after they’re played. This is handled with a palette swap, and redrawing pixels surrounding each note. It’s wildly expensive, but it looks nice, and fixes issues with static overlays on top of animated images.
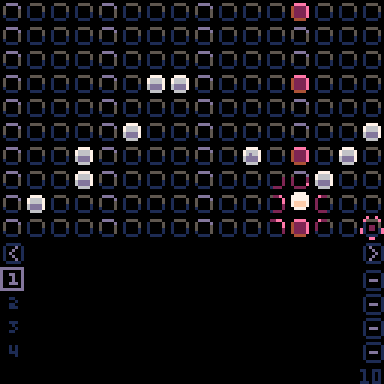
I’m doing this in a pretty simplistic way. For a much more performant (and technical approach), here’s a really cool article:
https://hackernoon.com/pico-8-lighting-part-1-thin-dark-line-8ea15d21fed7
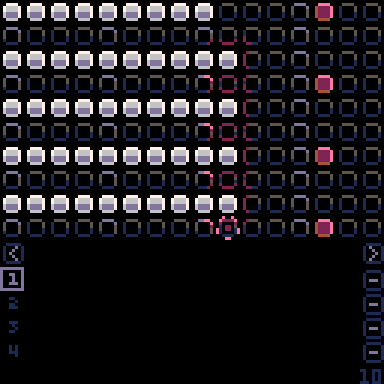
In the end, I used a simpler approach, using one level of lighting off to the sides of the
Particles
I started on some particle effects to make the visuals a little more engaging, but ran into further performance issues there. I put together a simple profiler to help track down the specifics.
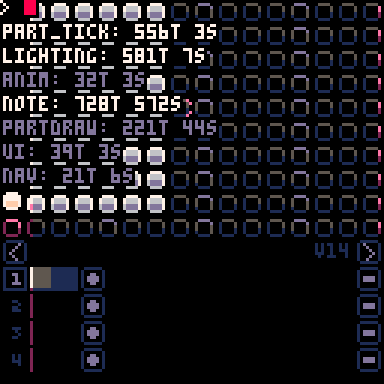
PICO-8, as a virtual console, has it’s own CPU limits distinct from the host system, and applies extra CPU cost to some operations.
The biggest takeaway here for me was: Limit expensive redrawing, limit deeply nested loops, limit overall particle counts (and make sure that count is up to date, and not from the last animation frame. Whoops)
I think these look nice still, but they’re big, slow and floaty, like each note is shaking down snow. Still nice, but I wanted a more explosive feel.
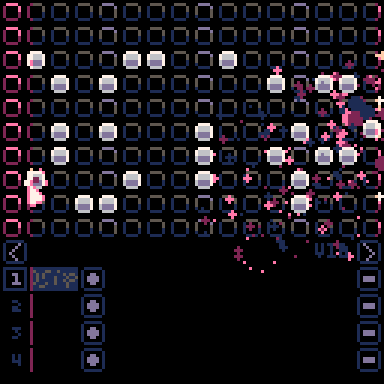
Here’s a less colorful, and more conservative version. Particles have more starting velocity, and fade faster.
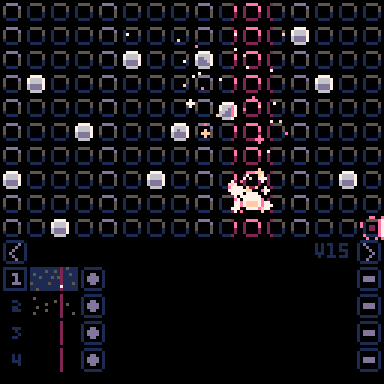
Here’s the final version. Notable changes here:
- Notes are always in front of the particles, and have a bit of an opaque outline around them, making them much more visible when a lot is happening on screen.
- Two or three contrast frames at beginning of the particle burst, making it more distinct and poppy.
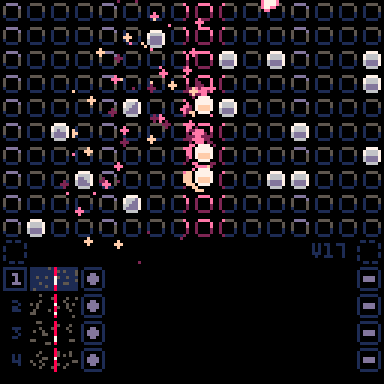
I recommend looking through (and supporting) this amazing pixel art resource: https://blog.studiominiboss.com/pixelart